-
Over 90 Years
industry expertise
-
Largest
facility & product range
-
Leaders
in the technology market
-
UK Based
service department
DD
FICEP is a leader worldwide for manufacturer of forging presses we has developed a revolutionary “DIRECT DRIVE” system for screw presses; this new type is called DD screw press and is based on the concept of the linear motor a very high performance motor that has been fully used in the field of CNC machine tools.
Ficep have now devised an “EXTREME HIGH TORQUE FRAMELESS MOTOR”, designed to drive directly the screw of the press.
This solution, besides being very simple from a construction point of view, makes the motor-flywheel group extremely, less sensitive to the vibrations and the strong decelerations it is subjected to with the impact effect when forging the piece on the die, furthermore, the high efficiency and the considerable dynamic performance typical of this linear motor, added to a latest generation of electronic drive, enables several advantages, both technological (accuracy, distortion capacity, repeatability) and economic (productivity, energy saving, reliability, maintenance).
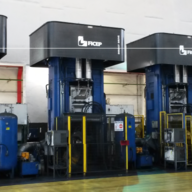
Tech Specs
DD | DD 12 | DD 40 | DD 50 | DD 68 | DD 85 | DD 110 | DD 140 | DD 190 | DD 270 | DD 400 | DD 560 | DD 750 | DD 1100 | DD 1600 |
---|---|---|---|---|---|---|---|---|---|---|---|---|---|---|
Screw diameter [mm] | 160 | 230 | 255 | 280 | 305 | 330 | 368 | 410 | 455 | 510 | 560 | 630 | 710 | 800 |
Max. continuous force [kN] | 4100 | 8500 | 10400 | 12800 | 14900 | 17500 | 21800 | 27000 | 33200 | 41600 | 50400 | 64000 | 80600 | 102400 |
Gross energy [kJ] | 12.5 | 60 | 80 | 108 | 154 | 177 | 240 | 331 | 445 | 652 | 860 | 1230 | 1700 | 2500 |
Max stroke per minute [no.] | 42 | 38 | 31 | 30 | 28 | 25 | 23 | 19 | 16 | 15 | 13 | 11 | 10 | 9 |
Ram stroke [mm] | 350 | 450 | 475 | 475 | 500 | 500 | 550 | 650 | 700 | 800 | 900 | 1000 | 1100 | 1250 |
Vertical clearance [mm] | 400 | 650 | 750 | 750 | 915 | 1100 | 1100 | 1200 | 1250 | 1400 | 1500 | 1700 | 1800 | 1800 |
Horizontal clearance [mm] | 500 | 650 | 750 | 750 | 1000 | 1070 | 1100 | 1290 | 1350 | 1400 | 1500 | 1630 | 1800 | 2000 |
The actual production of DD screw presses can reach the nominal force of 4.000 ton (max force 8.000 ton),
and recently, FICEP R&D in cooperation with his partner SIEMENS, are developing 2 new larger models, which will bring the nominal force up to 6.400 ton (max force 12.800 ton).
Now, FICEP’s R&D department is glad to introduce “state of the art” technology in this field, thanks to the latest version developed by SIEMENS using KERS technology (Kinetic Energy Recovering System).
Over several decades, screw presses have gained an important position in the forging industry, thanks to their application versatility, accuracy of the parts that can be achieved and reduced working cost; now with the introduction of the new generation of DD screw press, FICEP has amplified these advantages.
The main features which characterize the DD screw press and make it different, compared to other forging machines, are the following:
- Screw press with defined and controllable energy (similar to hammers, but 4 times more powerful) and without stroke limitation, compared to the crank press which is a machine with defined stroke and limited force and energy, whereas the hydraulic press is a machine with defined force.
- Absence of a fix bottom dead center, and as a consequence:
- No need to adjust the dies height
- Possibility to forge in a closed die
- High accuracy of the forged pieces thickness, which is only determined by the dies and not by the mass or temperature of the starting slug.
- The same accuracy is maintained in the time, as the thickness is not influenced by the machine temperature;
- Reduced set-up time;
- Possibility to carry out more forging stroke in the same die, allowing the realization of more complex pieces or with larger dimensions, in comparison with other presses having the same capacity;
- Not improper stops for the machine due to an excess of forged piece mass, or an insufficient temperature of the slug, or for a wrong adjustment of the press stroke.