-
Over 90 Years
industry expertise
-
Largest
facility & product range
-
Leaders
in the technology market
-
UK Based
service department
Steel Beam Drilling Lines
Used for structural steel section processing, multi-spindle drilling lines incorporate a selection of drilling tools to create a range of hole sizes and profiles in structural steel sections. The range of tools can be used for drilling, milling for slotted holes, notching, countersinking, tapping and scribing.
Ficep UK produces six different models of stand-alone CNC controlled multi-spindle drilling lines for the fabrication of structural steel. Here are some of the basic design features that are resident in our steal beam drilling lines.
Measuring
- Rack and pinion positioning and measuring achieves an accuracy level that is second to none
- The positioning accuracy is not affected by rust, scale, ice or snow on the section
- Automatic stock length measuring before the section is processed
- The positive rack and pinion system does not require calibration for changes in material type or conditions
Drill Spindles
Ball screw spindle feed with uniform feed rate for exceptional tool life and the ability to:
- Mill for slotted holes
- Countersink
- Tap
- Scribing
- Spindle speeds up to 5,000 RPM to maximize the utilization of carbide tools for drilling rates 10 times that of typical oil hole drills
- The drill spindle and head feed as one unit for maximum rigidity
- Coolant through the spindle or external coolant capability per the program
- The Ficep drill spindle like today's machining centers employs direct drive motors which eliminates the need for internal gears to reduce maintenance cost.
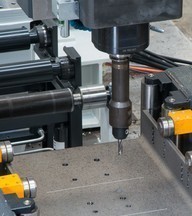
Tool Changer
- Automatic tool changing on each spindle
- When different hole sizes are required in a section or from one section to the next, the tool is changed as directed in the program
- Eliminates operator error
- When the drill requires replacement the software automatically changes the tool to a new drill of the same diameter
- The full range of spindle speeds is available for any tool that is loaded into the magazine
- The software automatically changes the required feeds and speeds based upon the tool that is loaded into the spindle
- The fixed spindle design, mechanical feed and synchronisation of the spindle feed and speed permits not just drilling but also:- scribing, milling for slotted holes, countersinking and tapping.
Control
All of the Ficep CNC lines feature a PC based CNC control with Ficep engineered software to ideally match the application for the drilling line.
- Low maintenance cost due to the use of a standard PC platform
- The Ficep software eliminates the requirement for additional hardware such as third party axis control boards, PLC hardware and encoder switching boards
The Ficep Windows based control is provided with the proprietary Ficep software for remote diagnostics through a phone connection or VPN.
Single Spindle Drills
A single spindle drilling machine offers a space-saving alternative to a multi-spindle drill line. Equipped with multiple tools, a single spindle drilling machine can carry out all drilling, scribing, countersinking, milling and tapping operations required for structural steel beams. Drilling machines can feature wireless controls to enhance operator productivity.
Structural Steel Beam Drilling
The modern day CNC structural drilling systems used in steel fabrication need to perform a whole range of cutting, shaping and drilling operations. Drill lines for steel beams can be single spindle stand-alone systems or multi-spindle lines incorporating a selection of tools for drilling, milling, countersinking, notching, tapping and scribing.
The most comprehensive line of CNC Structural Drilling Systems available in the market today!
As the drilling applications for structural steel are quite varied, Ficep has developed the most comprehensive product line of 34 different CNC drill line systems in the world today to provide the most productive and cost effective solution for your application. The Ficep drill line systems can be provided as a stand-alone CNC drill line system or in tandem with either a CNC controlled saw or a CNC controlled robotic coping system that are available with both plasma and oxy-fuel. The choice of “stand alone” system or full integrated automatic production line can be tailor made to suit customers’ choice.
Ficep has the right product for your business whether you need a single spindle CBC drill line or a spindle line with up to 18 different tools
Having difficulty finding employees for fitting and layout? Want to increase the productivity of your layout staff 6 fold?
Over 50 years ago beam punch lines were developed to eliminate the requirement to manually layout the hole locations which greatly reduced the amount of manual layout that was required. Unfortunately since this development, almost a half of a century ago, nothing else has really changed to reduce the most expensive manual operation a fabricator faces.
Ficep has introduced and patented (US Patent 7974719 granted7/5/11) the first major enhancement in this process in the past half of a century by automatically bringing in the scribing information that indicates the layout locations for subsequent fitting. This information can be extracted as a single XML file with our software that not only generates the part size and hole location data, but it also creates automatically the CNC machine program to scribe all the required layout information on the main member (four sides) and on the detail parts.
Once the beam hits the fitting area, your fitter matches the part number reference on the main member with the same part number on the detail part. The scribing lines indicate the placement location and there is even orientation scribe marks on the plate and the main member so your fitter knows how to orient the part!
Existing case studies show that when using this new technology, the amount of manual layout that is required is reduced 6 fold! This latest development from Ficep, the technology leader, gives you the opportunity to not only reduce your man hours per ton but to also greatly increases your tonnage capability.